Rick
(Technical Evangelist)
7
Chatting with the team, consensus is this looks like a power / tube / temperature issue. A couple of thoughts that might be worth review
:
Another potential workaround, providing additional shapes outside the intended output used to get the tube energized and firing sooner:
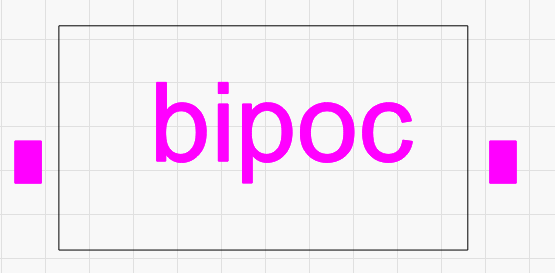